Locally sourced frac sand gets the job done at a discount
Last week, Alpine Silica, a private supplier of frac sand, announced that it will open two new frac sand projects—one in Van Horn, Texas and the other in Fay, Oklahoma, further adding to its existing sand portfolio.
Alpine estimates that the Oklahoma plant and the Van Horn facility will each produce about three million tons of frac sand per year. Alpine expects the Oklahoma project will break ground within the next 30 days and will have a 6-month construction period. Van Horn will be on a similar schedule.
Where is the local sand?
There are currently 32 operating frac sand facilities in Texas. Most are in the Kermit, Voca, and Van Horn areas.
In-basin sand operators include Alpine Silica, Hi-Crush Partners LP (NYSE: HCLP), Black Mountain Sand, US Silica Holdings Inc (NYSE: SLCA), Vista Proppants and Logistics, Covia (NYSE: CVIA), Emerge Energy (NYSE: EMES), and Aequor.
Emerge Energy subsidiary Superior Silica Sands announced last week that it had secured a 25-year lease agreement that encompasses mining rights on 600 acres of land located approximately 60 miles northwest of Oklahoma City in Kingfisher County. Emerge said it expects volume to be about one and a half million tons per year, and it’s planning a 2018 startup for the facility.
In May, Preferred Proppants, or Preferred Sands, said it had begun construction of an in-basin frac sand mine and facility in Oakwood, Oklahoma. The mine is expected to come online in the third quarter of 2018 and will serve the prolific SCOOP, STACK and other Midcontinent formations. Previously Preferred had opened a mine in South Texas and an expansion into West Texas.
In the beginning, there was only Northern White from Wisconsin and Minnesota mines
The shale boom began with operators fracing only with sand sourced from Wisconsin and Minnesota—Northern White sand. Northern White was preferred for its strength in successfully holding open fissures during fracing operations, but it comes with a price not only for its physical qualities, but to pay for the cost of transporting millions of tons of the heavy material by rail to Texas or Oklahoma or Louisiana.
As cost-cutting became the oil and gas industry’s uniform of choice in the downturn, many operators turned to local, in-basin sand because it’s cheaper and gets the job done. One or two oil and gas companies opened their own in-basin mines.
Pioneer Natural Resources (ticker: PXD) saw the benefits long before the downturn. In April of 2012 Pioneer acquired a large U.S. industrial sands company, which was renamed Premier Silica and later became known as Pioneer Sands in June 2017. This move gave Pioneer a supply of low-cost and logistically advantaged brown sand to use for its own fracture stimulation requirements in the Permian Basin.
Texas sand is located in dunes, making it easier to mine than Wisconsin sand locked in sandstone deposits, IHS analyst Samir Nangia told the AP in January.
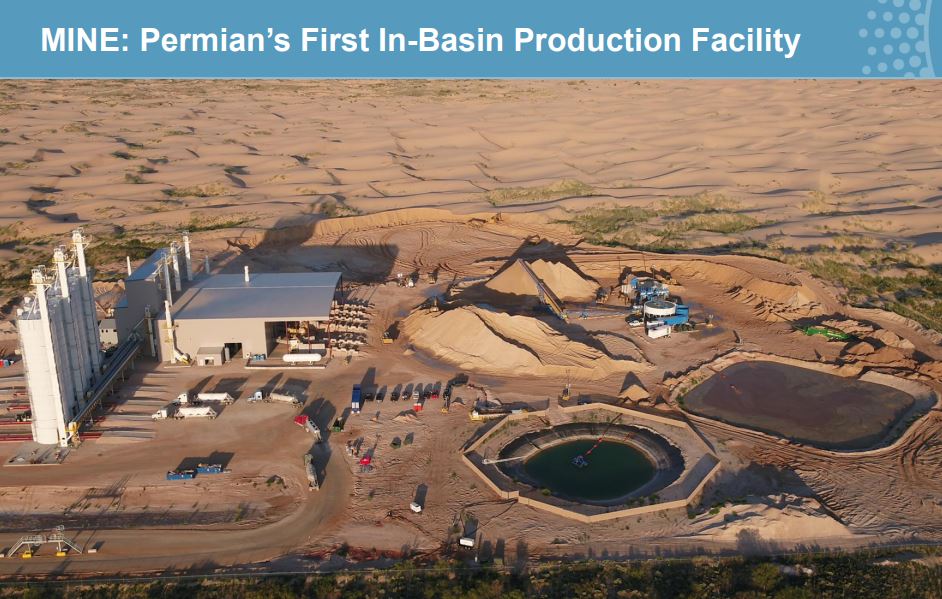
“You wash it, you dry it, you put it on a truck and you send it where it needs to go,” Nangia told the AP. “You don’t need a rail load out terminal, you don’t need to do any blasting, you don’t need to do any heavy moving, and then on top of that you only need to truck it 50 miles to 75 miles.”
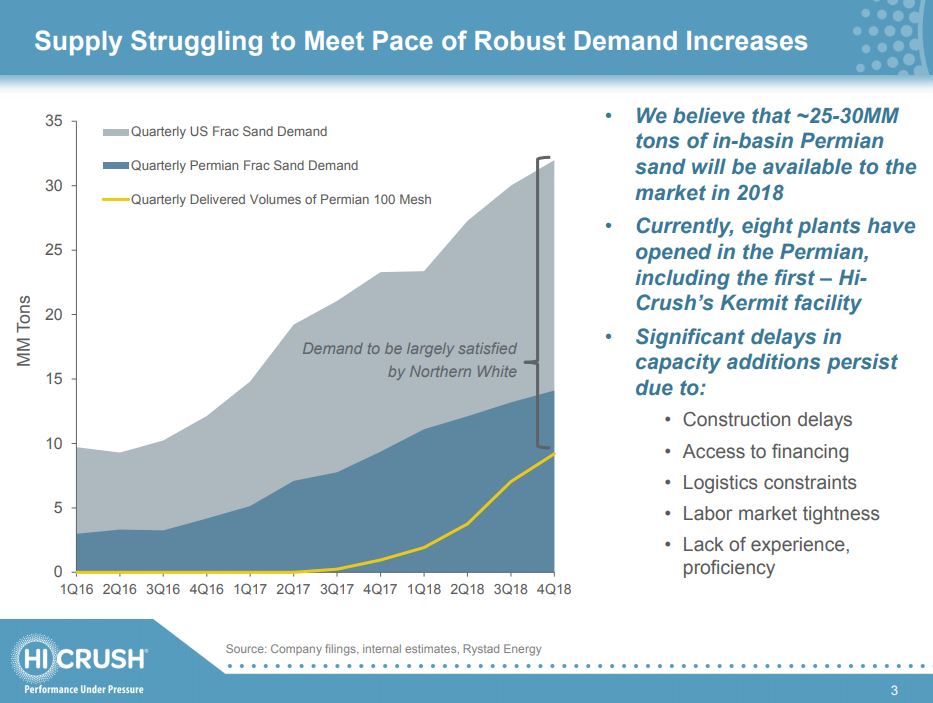
After being battered with the rest of the oilservice sector in the downturn, proppant suppliers today are seeing a return to busy times.
Demand for sand from the Midwest and demand for local sand in Texas has risen to pre-downturn levels with the return of growth to drilling and completions in 2017 and 2018, and also because of the trend of many companies to use much more sand per foot in their completion schemes.
The return to high demand is “partly what sent Wisconsin sand companies scrambling to build on the Union Pacific line, which offers a direct route to the Permian,” the La Crosse Tribune reported in March.
“Sand producers invested hundreds of millions of dollars in rail terminals where they can store hundreds of cars and build fully-loaded unit trains to trim shipping costs. Still, getting a ton of sand to a well site in Texas can add more than $80 in delivery costs to the $44 price.”
Sand M&A
On June 1, two large industrial materials providers—Unimin and Fairmount Santrol closed their merger, resulting in a new public company that controls nearly a dozen Wisconsin facilities in addition to three of Minnesota’s industrial sand operations. The combined companies operate under the name Covia (NYSE: CVIA with 50 plants and 94 operating terminals, including a large number of energy-focused sand operations in Texas and Oklahoma.
Hi-Crush Partners (ticker: HCLP) is another player in-basin. Hi-Crush owns and manages four mines supplying Northern White sand to the industry. In 2017 the company opened the Permian Basin’s first in-basin production facility at Kermit, Texas.
As long as oil prices stay up, and laterals get longer and completions intensify, proppant will be in high demand
Demand for sand is not just in Texas and Oklahoma. In Louisiana’s Haynesville shale play, for example, last summer Goodrich Petroleum (ticker: GDP) initiated a new completion design using 3,000-5,000 lbs. of proppant per foot, versus the prior design which utilized approximately 1000 lbs. of proppant per foot. Combine that with longer laterals—up to 10,000 feet—the demand for sand is only going to get stronger.
Goodrich Chairman and CEO Walter Goodrich said earlier in the year that its participation in 10,000 ft., high-proppant wells had exceeded expectations.
As operators tweak well completion formulae in different plays, the concentration of sand will vary, but the trend since the beginning of the shale boom has been moving in the direction of longer laterals, more perf stages and more sand per foot.
Most wells need about 12 million pounds of sand, according to Fairmount Santrol product director Brian Goldstein who spoke at the EnerCom Oilfield Tech and Innovation Conference in Dallas in March. “That means bringing 250 truckloads or 50 railcars’ worth of sand to a wellbore,” Goldstein said.
With Texas home to more than half of all U.S. working drilling rigs, and the majority of those engaged in drilling horizontal wells, the demand for in-basin sand isn’t expected to dry up anytime soon.
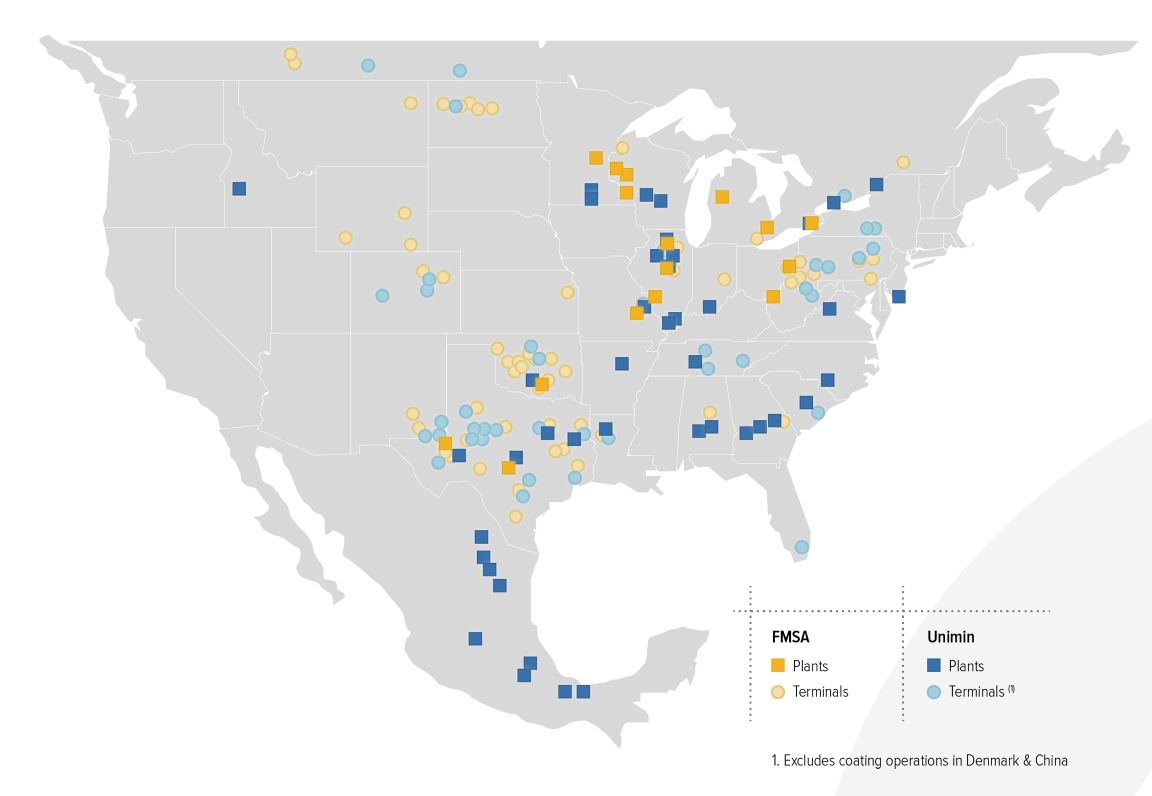