From a farmer’s grain bin to the massive reaches of the frozen north of Canada, where virtually every fuel and metal on Earth is extracted, what is the most sought-after commodity?
Heat. Particularly Flameless Heat.
A couple of years ago, Artic Therm (ATI)-- a wholly owned subsidiary of Alberta-based Enterprise Group (E: TSX) began expanding applications for its flameless heat business. That gamble has resulted in roughly a 25% growth in business year over year. (Ask any fireman and he will tell you fighting a fire in freezing weather is the ultimate nightmare).
With approximately 150 units, these robust and versatile units from retail size to those large enough to heat and condition massive lengths of pipelines and require an operator 24/7.
Hands up! Who Likes Wet Grain?
No one.
Drying grain, thawing frozen equipment, heating a barn or living quarters or prepping a pipeline section; it is pretty much the only economical way to keep things warm and dry. Temperatures that can reach minus 50, and that’s before the addition of the almost constant deadly wind chills.
Let’s chat about Grain Drying.
The traditional process; combine, bin, remove, dry with a natural gas dryer. Downsides? Time and portability. The new way, combine, bin, turn on aeration fan, hook up Artic Therm Dryer. Each grain has or is reduced to an acceptable level of moisture. The faster the excess can be removed, the longer the quality and salability are maintained. Check out the chart below and the nifty truck pic:
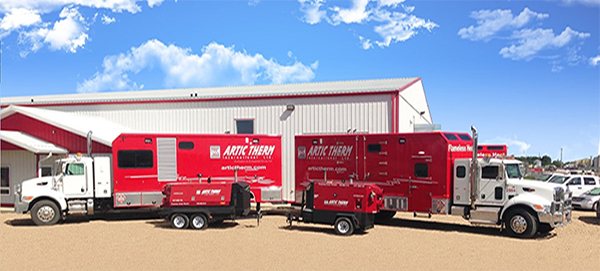
Weight of water in barley at various moisture contents
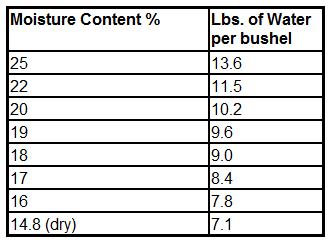
Utilizing one of Artic Therm’s 150 flameless heaters, with maximum heat ranging from 500K btu to just over 3 million btu, the goal is to add the dryer and upping the efficiency of the bin’s aeration fan. By speeding up drying by a point (1%) a day, the process is not only cost effective but gets the grain to market faster thereby securing better prices. The barley chart above delineates the moisture reduction.
As well, since grain can be binned all over a large farm, portability is critical. The stakes are high; if not done correctly, a lucrative crop will quickly be reduced to worthless seed.
What are the costs per bushel for this grain drying?
With a monthly rental cost in the low four figures, the cost of retaining quality top price grain is worth the incremental heating cost, which works out to pennies a bushel. If the process gets the good product to market faster, even slightly, it’s a small price to pay.
Again, this is probably best illustrated with an example calculation using several assumptions. Keep in mind that this example includes fuel costs only and does not include the additional costs of labor, electricity, grain handling, depreciation, and other less direct costs.
- 1 gigajoule (GJ) = 1,000,000 BTU (1 GJ/1,000,000 BTU)
- Natural gas costs $5/GJ
- Weight of water to remove: 9.6 lb. - 7.1 lb. = 2.5 lb./bu
- 2.5 lb./bu X 2000 BTU/lb. = 5000 BTU/bu needed
- $5/GJ X 1GJ/1,000,000 BTU X 5000 BTU/bu = $0.025/bu
Take out the Nat Gas portion and drying costs per bushel drop dramatically
“The drying concept is not actually to blow massive amounts of heat into the grain but to make the aeration fans in the bins more efficient,” states Desmond O’Kell SVP of Enterprise. “While an aeration fan will eventually dry the grain, and/or with the use of expensive natural gas, our units vastly shorten drying time and more cost-effectively allow our client to get the best or desired price for the crops whether going to market immediately or resting in a grain silo. Like most products at our subsidiaries, management keeps assets in top shape and rented. That means coming up with a myriad of uses that both maximize rental time and ultimately revenues.”
Why Should Investors Care About Wet Grain?
They shouldn’t. They should care about dry grain.
With significant growth rates, ATI is quickly educating farmers to eschew their healthy and usually wise resistance to new processes.
“Once a cereal crop is harvested, it may have to be stored for a period before it can be marketed or used as feed or seed. The length of time cereal can be safely stored will depend on the condition it was harvested, and the type of storage facility being utilized. Grain binned at lower temperatures and moisture contents can be kept in storage for longer periods of time before its quality will deteriorate. The presence and build-up of insects, mites, molds and fungi, which are all affected by grain temperature and grain moisture content, will affect the grain quality and duration of grain storage.” (Alberta Agriculture and Forestry)
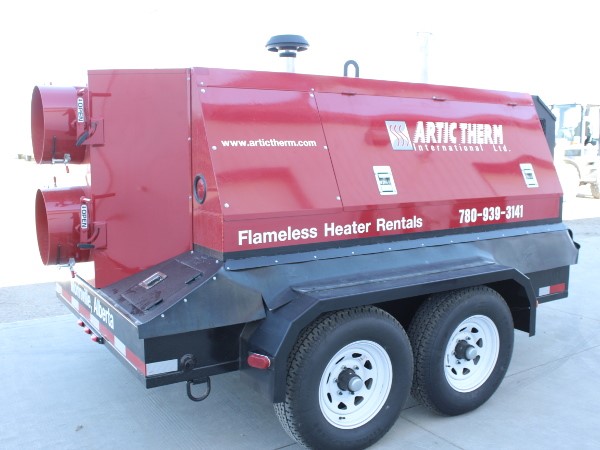
Bottom Line
Using heat to make the drying process more efficient is a relatively new process but quickly becoming an impressive profit centre. There are very few companies who have made an ATI size commitment and the Company is arguably the most significant player. Even ATI/Enterprise don’t know the exact size of what is undoubtedly a massive market. The Company is confident that as efficacy of the process spreads, the current and initial 25% year over year growth rate should climb dramatically. From an idea born at ATI to generate revenues during the 2015 downturn, grain drying is looking to become a significant revenue generator; along with all the other necessary uses of this unique flameless application.
Harvest is looming, and the Company is already seeing increased quote requests over last year.
Farmers and investors are not dissimilar. Those that are successful watch over their investments and find the best ways to maximize revenue and profits. It’s healthy that both are somewhat skeptical of new processes, but as Grain Drying is already a success and has potentially a massive growth path, it will become mainstream soon.
Almost forgot: Using the traditional drying methods, the aeration fan pulls out the moisture which tends to gather on the inside roof of the bin; meaning the drying takes longer without an ATI product. As a result, the traditional process can result in the first few feet of the top grain becoming wet, moldy and uneconomic. With the dryer combined the aeration fan(s), the result is a much higher volume of dry, saleable grain.

Disclaimer: Nothing in this article should be considered as personalized financial advice. We are not licensed under securities laws to address your particular financial situation. No communication by our employees to you should be deemed as personalized financial advice. Please consult a licensed financial advisor before making any investment decision. This is a paid advertisement and is neither an offer nor recommendation to buy or sell any security. We hold no investment licenses and are thus neither licensed nor qualified to provide investment advice. The content in this article is not provided to any individual with a view toward their individual circumstances. Baystreet.ca has been paid a fee of one thousand two hundred dollars for Enterprise Group advertising. This compensation constitutes a conflict of interest as to our ability to remain objective in our communication regarding the profiled company. Because of this conflict, individuals are strongly encouraged to not use this article as the basis for any investment decision. While all information is believed to be reliable, it is not guaranteed by us to be accurate. Individuals should assume that all information contained in this article is not trustworthy unless verified by their own independent research. Also, because events and circumstances frequently do not occur as expected, there will likely be differences between any predictions and actual results. Always consult a licensed investment professional before making any investment decision. Be extremely careful, investing in securities carries a high degree of risk; you may likely lose some or all of the investment.