You don’t need to consult an engineer to know each and every shale play is different.
Generating the highest possible recovery is a constant chess game run by E&Ps around the globe, and every play has something else to offer. The trend of increasing fracturing stages and proppant/sand use per stage was a popular topic in breakout sessions at EnerCom’s The Oil & Gas Conference® 19 last month. The intensive development is paying off for operators. In the Q2’14 conference call for Core Laboratories (ticker: CLB), David Demshur, Chief Executive Officer, said, “You have operators out in the Permian Basin that, on average, spend $1 million more per well, but they’re yielding an additional 400,000 barrels in ultimate estimated recovery. For me, that’s a no-brainer.”
The Varying World of EOR Recipes
Enhanced oil recovery (EOR) methods can range from traditional ways like CO2 flooding to more unconventional ways, like reinjecting extracted natural gas. Demshur added that CLB is “looking at alternating steam and gases for enhanced oil recovery, both in the Bakken and in the Eagle Ford.”
Flying below the EUR-boosting radar is another little-known asset: foam from liquid nitrogen. A recent study conducted by Rice University revealed “In tests, foam pumped into an experimental rig that mimicked the flow paths deep underground proved better at removing oil from formations with low permeability than common techniques involving water, gas, surfactants or combinations of the three.”
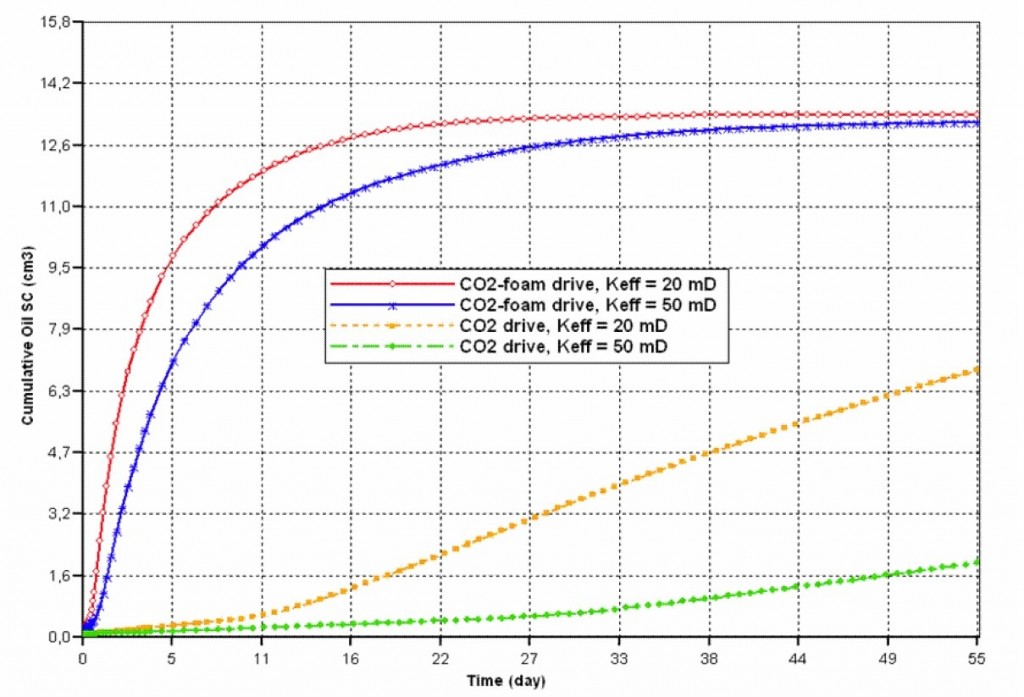
The Benefits of Foam
In a study in October 2013, George Hirasaki, a Rice research professor of chemical and biomolecular engineering, explained the process: “We’re trying to understand how foam behaves in porous media because it is a way of making gas act like a more viscous fluid. Normally, gas has very low viscosity and it tends to flow through rock and not displace oil and water. Once it finds a path, usually along the top of a reservoir, the rest of the gas tends to follow. If there were some way to make gas act more like a liquid, to make it more viscous, then it would contact much more of the reservoir and would push the fluids out.”
Rice’s latest study revealed foam extracted a total of 74.9% of oil from low-permeability regions within four minutes. A mixture of water and gas, on the other hand, removed 47.0% of the hydrocarbons and water flooding removed just 1.7% in the same time frame. Hirasaki participated in this project along with associate professor Sibani Lisa Biswal, who concluded “Because foam acts like a more viscous fluid, it’s better able to plug high-permeable regions and penetrate into less-permeable regions.”
Foam Success Stories
Low pressure wells, in particular, are ideal for the use of foam injection.
Halliburton (ticker: HAL) provided information on September 3, 2014, on a well revitalized by the use of a CO2 foamed frac fluid. The 14,000 ft. well exploiting the Morrow formation in Oklahoma declined from an IP rate of 20 MMcf/d to 1 MMcf/d before being killed after a failed methanol treatment. HAL used 13,000 gallons of the frac fluid and resulted in production jumping back online at 8 MMcf/d. The well was still producing at 3 MMcf/d three months later, equaling $330,000 in gross revenue.
A story published by the American Oil & Gas Reporter in February 2014 said energized fluids improved well performance by as much as 2.1x, compared to nonenergized solutions. The use of foam reduces the need for water, which can swell clays and restrict permeability. The story adds: “Adding CO2 or N2 to the fracturing fluid reduces the need for gelled fluid, and therefore, the amount of residual gel left in the proppant pack. And as issues continue to arise around water usage and management in hydraulic fracturing, adding or using CO2 or N2 can reduce or even eliminate water volumes, greatly reducing the challenges associated with acquiring, transporting, storing, recovering and recycling or disposing of water.”

Not to the Finish Line… Yet
So while foam can increase EURs when used correctly and reduce the need for water treatment, its cost and reliability have prevented it from becoming a mainstay in field operations.
In 2011, the Department of Energy committed $12.4 million to 11 different research projects aimed at increasing hydrocarbon recovery while reducing the environmental footprint. Some projects are still underway, and the final review from a University of Texas revealed, in short, that further research is needed in order to provide foam stability.
Mukul Sharma, a professor of petroleum, geosystems and chemical engineering at the University of Texas, said, “I personally have difficulty seeing how it could be commercially applied, given the cost and difficulty in handling the fluid.”
Foam can also dry out as it moves through the formation, ultimately reducing its viscosity and limiting the amount of affected regions. A report by Schlumberger (ticker: SLB) also said foam, when in a CO2 state, can vaporize in high temperature environments.
In an interview with the Houston Chronicle, Ramanan Krishnamoorti, a professor of petroleum engineering at the University of Houston, said more tweaks need to be made. Liquid nitrogen does not have the energy capacity of water, and therefore has difficulty moving the sand or proppant for well completions.
Krishnamoorti said oil field service companies have reported some success with waterless fracturing technologies, “but never where they’re comparable to hydraulic fracturing.”
A study conducted by the Society of Petroleum Engineers believes the use of foam has a future, but is not ready for full-scale use at this time. “The results are promising at laboratory scale,” the Society said in its findings. “More tests are needed to show the ability of foam to improve conformance for better volumetric sweep efficiency. Although this technology is still in its early development, some operators have expressed interest in limited field testing.”
[sam_ad id=”32″ codes=”true”]
Important disclosures: The information provided herein is believed to be reliable; however, EnerCom, Inc. makes no representation or warranty as to its completeness or accuracy. EnerCom’s conclusions are based upon information gathered from sources deemed to be reliable. This note is not intended as an offer or solicitation for the purchase or sale of any security or financial instrument of any company mentioned in this note. This note was prepared for general circulation and does not provide investment recommendations specific to individual investors. All readers of the note must make their own investment decisions based upon their specific investment objectives and financial situation utilizing their own financial advisors as they deem necessary. Investors should consider a company’s entire financial and operational structure in making any investment decisions. Past performance of any company discussed in this note should not be taken as an indication or guarantee of future results. EnerCom is a multi-disciplined management consulting services firm that regularly intends to seek business, or currently may be undertaking business, with companies covered on Oil & Gas 360®, and thereby seeks to receive compensation from these companies for its services. In addition, EnerCom, or its principals or employees, may have an economic interest in any of these companies. As a result, readers of EnerCom’s Oil & Gas 360® should be aware that the firm may have a conflict of interest that could affect the objectivity of this note. The company or companies covered in this note did not review the note prior to publication. EnerCom, or its principals or employees, may have an economic interest in any of the companies covered in this report or on Oil & Gas 360®. As a result, readers of EnerCom’s reports or Oil & Gas 360® should be aware that the firm may have a conflict of interest that could affect the objectivity of this report.