First polyethylene shipment from mega-plant is slated for export from Houston in October
ExxonMobil (ticker: XOM) Chemical Company started production on the first of two new 650,000 tons-per-year high-performance polyethylene lines at its plastics plant in Mont Belvieu, Texas.
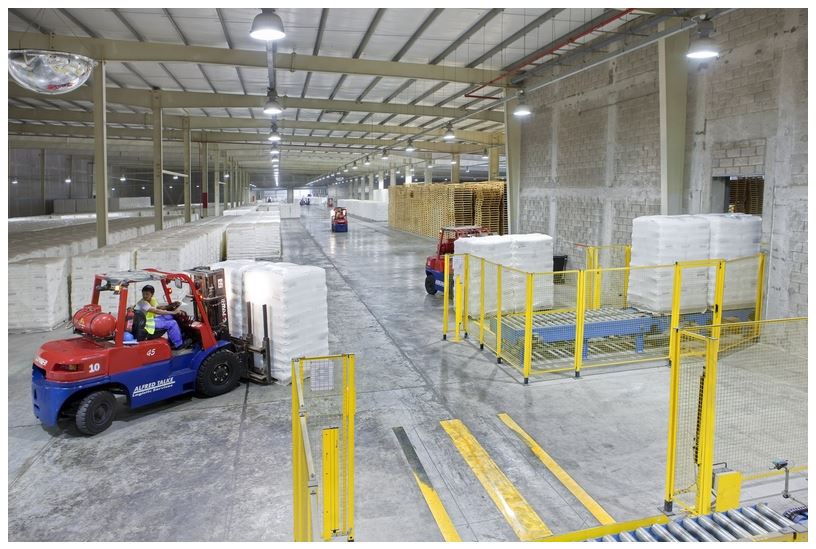
The full project, part of the company’s multi-billion dollar expansion project in the Baytown area and ExxonMobil’s broader Growing the Gulf expansion initiative, will increase the plant’s polyethylene capacity by approximately 1.3 million tons per year.
One of the natural gas liquids, ethane, is largely used in ethylene-cracking plants in the production of ethylene for plastic production.
The two major components of ethylene production are ethane and naphtha. EIA notes that there is a shift occurring in the production of ethylene through the shift from heavier naphtha to lighter ethane. EIA says, “Naphtha, a hydrocarbon that contains mostly molecules with 5–12 carbon atoms, is one of the lighter components produced by refining crude oil. It is a much heavier feedstock than ethane or propane, which respectively consist of hydrocarbon molecules with 2 or 3 carbon atoms. All ethylene projects currently planned for the United States are designed to consume light feed, predominantly ethane, for the production of ethylene.” Plastics manufacturing is a major global industry, and the U.S. plastics industry is expecting a sea change brought on by the emergence of shale gas production. This is borne out by the planned new and expansion plans for plants to make polyethylene in the U.S.
The Mont Belvieu plant capacity will total more than 2.5 million tons per year, making it one of the largest polyethylene plants in the world. These performance polyethylene products will deliver significant sustainability benefits enabling lighter weight higher performance packaging, lower energy consumption and reduced emissions, Exxon said in a statement. At peak, the site will be able to ship more than 200 containers a day from Houston, Exxon said.
ExxonMobil Chemical President Neil Chapman said his company is addressing a growing global demand for high-performance polyethylene products worldwide.
ExxonMobil is planning to invest more than $20 billion over 10 years to build and expand manufacturing facilities in the U.S. Gulf region. Exxon says that the projects are expected to create more than 45,000 jobs, including more than 12,000 full-time jobs. The expansion covers 11 major chemical, refining, lubricant and liquefied natural gas projects along the Texas and Louisiana coasts.
ExxonMobil’s Baytown area is the largest integrated petrochemical complex in the U.S. Exxon’s Baytown operations were founded in 1919. The complex has 3,400 acres along the Houston Ship Channel and includes a refinery, chemical plant, olefins plant, plastics plant and a global technology center.
Shell also building new ‘mega-cracker’
ExxonMobil is several years ahead of its rival Dutch oil major Shell (ticker: RDS.A), which will become a serious head-to-head U.S. competitor in the polyethylene production business, once Shell completes its own mega petrochemical project in Beaver County, Pennsylvania. The Shell plant is projected to begin principal construction in early 2018.

Shell Chemical Appalachia LLC took the final investment decision in June 2016 to build its major petrochemicals plant near Pittsburgh. The plant will consist of an ethylene cracker with a polyethylene derivatives unit. Main construction will start approximately 18 months after final investment decision, with commercial production expected to begin early in the next decade.
Where the gas for Shell is sourced – Marcellus and Utica producers
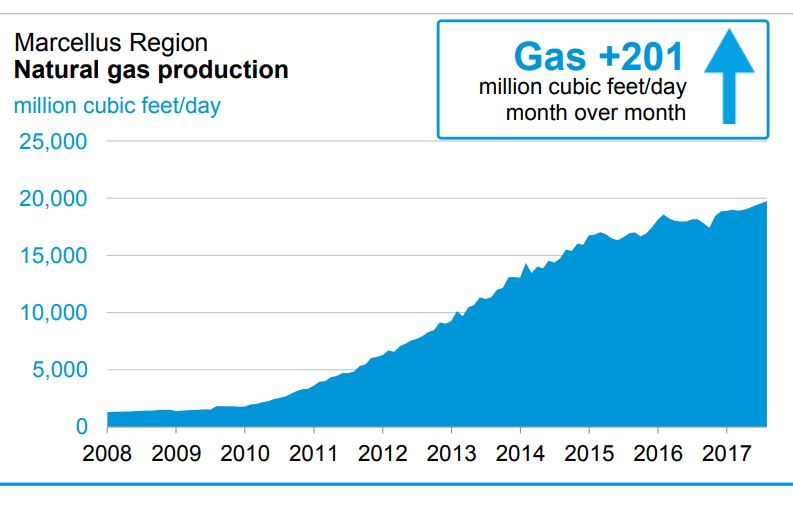
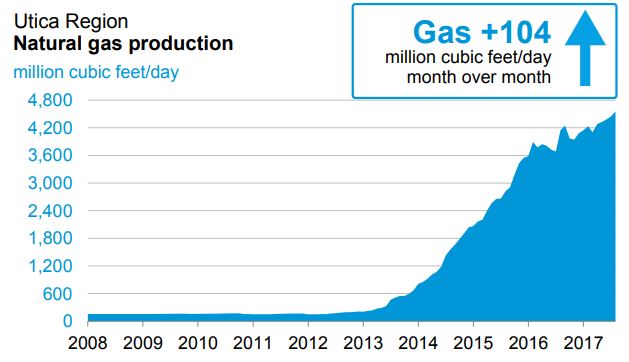
The plant will use low-cost ethane from shale gas producers in the Marcellus and Utica basins to produce 1.6 million tonnes of polyethylene each year. Polyethylene is used in many everyday products, from food packaging and containers to automotive components.
The facility will be built on the banks of the Ohio River in Potter Township, Beaver County, about 30 miles north-west of Pittsburgh.
Shell says that, as a result of its Beaver County plant’s close proximity to a source of natural gas—Marcellus and Utica producers—it will benefit from shorter and more dependable supply chains, compared to supply from the Gulf Coast. Shell says more than than 70% of North American polyethylene customers are within a 700-mile radius of Pittsburgh.
Another plant for Texas
ExxonMobil and Saudi Arabian chemical company SABIC announced in April of this year the selection of a site in San Patricio County, Texas, siting the plant near Corpus Christi, for their proposed petrochemical plant joint venture. First announced in July 2016, this complex is a joint venture between ExxonMobil Chemical and Saudi Arabia Basic Industries Corporation, SABIC, Saudi Arabia’s foremost chemical company. The Corpus Christi plant could cost as much as $10 billion, according to the Houston Chronicle.
A large ethane steam cracker capable of producing 1.8 million tonnes of ethylene per year would feed a monoethylene glycol unit and two polyethylene units. Ethylene and its derivatives are primary building block of many plastics.
ExxonMobil CEO Darren Woods commented in a press release, “We are using new, abundant domestic energy supplies to provide products to the world at a competitive advantage resulting from lower costs and abundant raw materials. In this way, an upstream technology breakthrough has led to a downstream manufacturing renaissance.”
Where the gas is sourced for Texas polyethylene plants: Eagle Ford, Permian, Haynesville
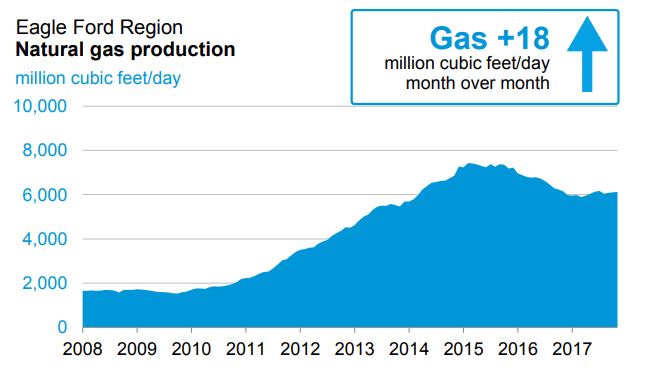
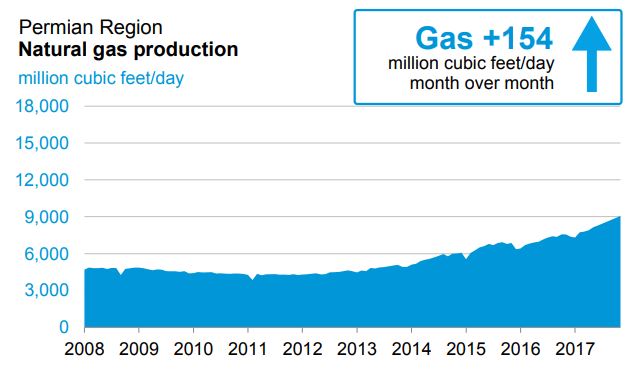
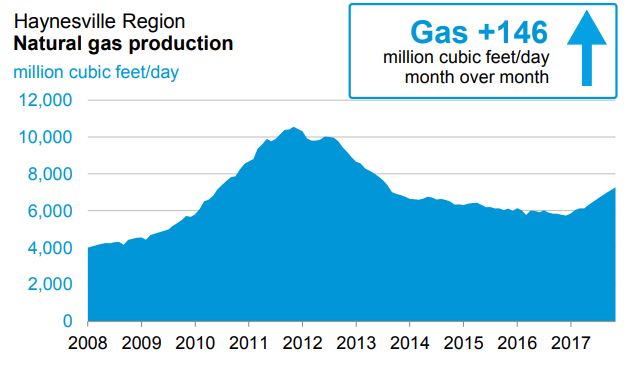